Relevant Applications
VIPs can be used in many important fields.
Vacuum Insulation Panels (VIPs) are ultra-thin, high-performing insulants that can be up to 20 times more effective than traditional insulation products.VIPs provide energy efficiency and space benefits for:
- Buildings;
- Home Appliances;
- Refrigerated Transportation Systems, including COVID-19 vaccines; and
- Any other Applications requiring Low Energy Loss from heat transfer.
The first VIP was made in 1930 from a porous material enclosed in rubber. In the 1950s, a glass wool core was welded to a steel panel. Nanostructured materials began to appear in the 1960s. The development of VIPs intensified and the first VIPs made of precipitated silica began to appear in the 1990s.
The principles of Vacuum Insulation have been known for around 100 years and have been used in appliance design for many decades. Now materials science has advanced and attention on the energy efficiency of buildings has increased. It follows that VIP products are being broadly applied in many industries where they were not previously used.
How are VIPs built?
A Vacuum Insulation Panel consists of a rigid, highly-porous core material encased in a thin, gas-tight outer envelope. The envelope is evacuated and sealed to prevent outside gases from entering the panel. The combination of porous material and the vacuum results in an extremely high thermal resistance. The thermal resistance allows for thinner insulation in applications where space is at a premium.
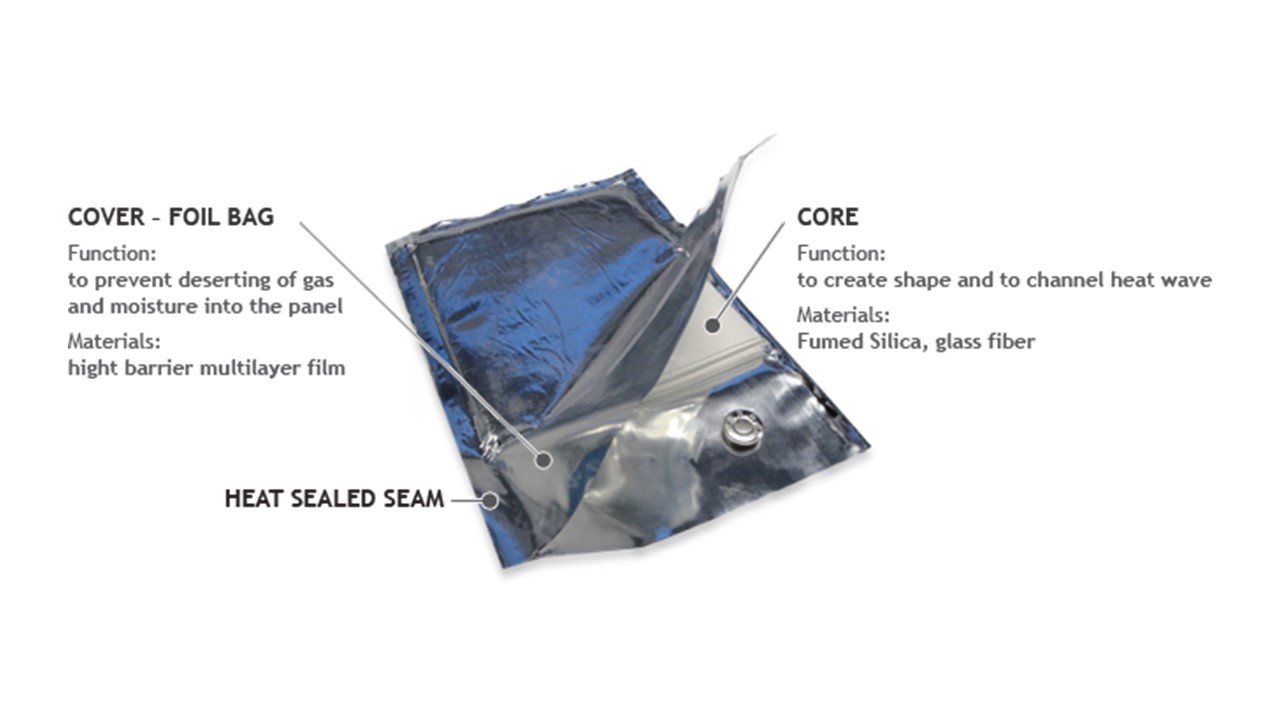
Core materials for VIPs
Core Materials for VIPs require a completely open-porous structure to allow evacuation. These materials must have a sufficiently high compressive strength to withstand the mechanical pressure load. Core material classes basically comprise three structures as microporous powders, fibres and foams.
Each structure has its inherent solid mechanical properties. The minimum density to withstand atmospheric pressure loads is distinctive. The same is valid for the centre of panel (COP) value for the thermal conductivity, which depends on the solid backbone of the core material. The core material should have the lowest possible thermal conductivity to ensure the VIP’s best performance.
Optimum materials have a microporous structure and are able to absorb humidity. Otherwise, getters have to be added. The most common core materials are fumed silica and glass fibres. In a few cases open-cell polymer foams, such as special polyurethane or polystyrene foams, are used.
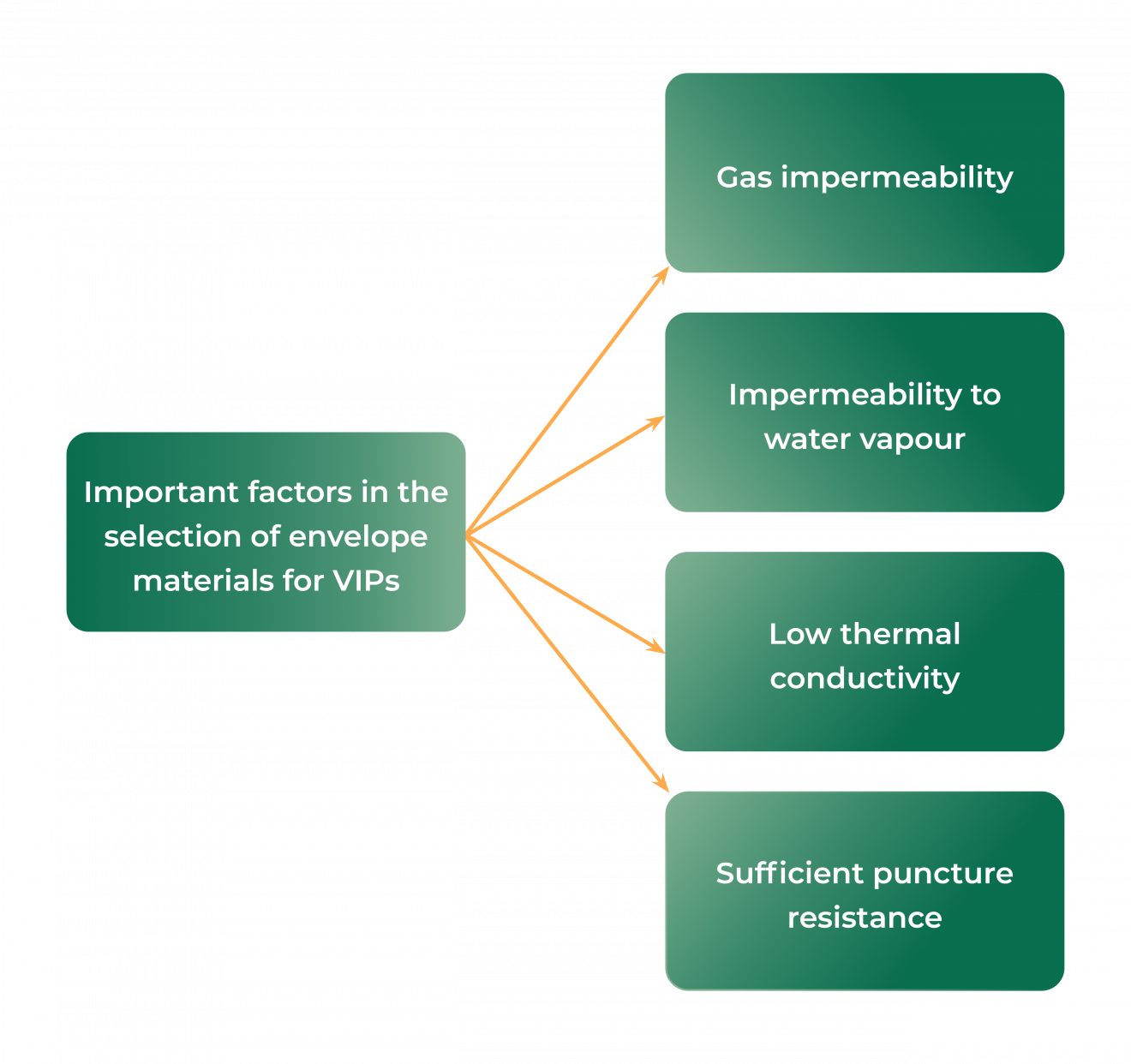
VIP envelope materials
Gas impermeability is the main factor influencing the selection of envelope materials for VIPs. In terms of a VIP’s life expectancy, its impermeability to water vapour is also important. Furthermore, a low thermal conductivity is also vital in order to keep the thermal bridge effect as low as possible along the edges of the panels. Because of the mechanical loads that occur during construction, the envelope materials should also have sufficient puncture resistance.
The envelope materials used for thermos flasks are also generally suitable for flat VIPs. These materials are namely stainless steel, aluminium and glass. In combination with filler materials such as foams and fibres, only these materials achieve the required high gas impermeability. High gas impermeability is the requirement for durable products. Most manufacturers use aluminium-metallised high barrier plastic laminates, aluminium composite films and stainless steel films or sheets to provide the VIP envelopes.
Advantages of VIPs
The thermal conductivity of a well-evaluated dry VIP with a fumed silica core is about 0.004 W/(m•K) after production. It is about 0.020 W/(m•K) at ambient pressure. By comparison, thermal conductivities of conventional insulation materials are typically between 0.030 and 0.040 W/(m•K).
Vacuum Insulation Technology provides:
- Extremely low insulation thicknesses (10 mm to 25 mm), increasing the volume capacity of applications for which a lack of space for insulation thickness is an issue. Moreover, the performance is stable and long-term thermal when panels are installed correctly and protected from damage and penetration.
- High-performance thermal insulation panels have a thermal conductivity 8 to 10 times lower than other conventional insulation materials (3 mW/(m•K). In addition, it is possible to have a new design and construction.
Estimations of the payback period (PBP) should include the value of the floor space made available by the thinness of the VIPs. Construction materials must have extremely long service lives.
VIPs reach the end of their service life when the gas pressure rises above 50 to 100 mbar. For this reason, much research and development is focused on the envelope of the VIP. Further research into panel construction could maximise the service life cycle to many decades or even a century.