VIP technology used in façade insulation of the Grand Tower Frankfurt
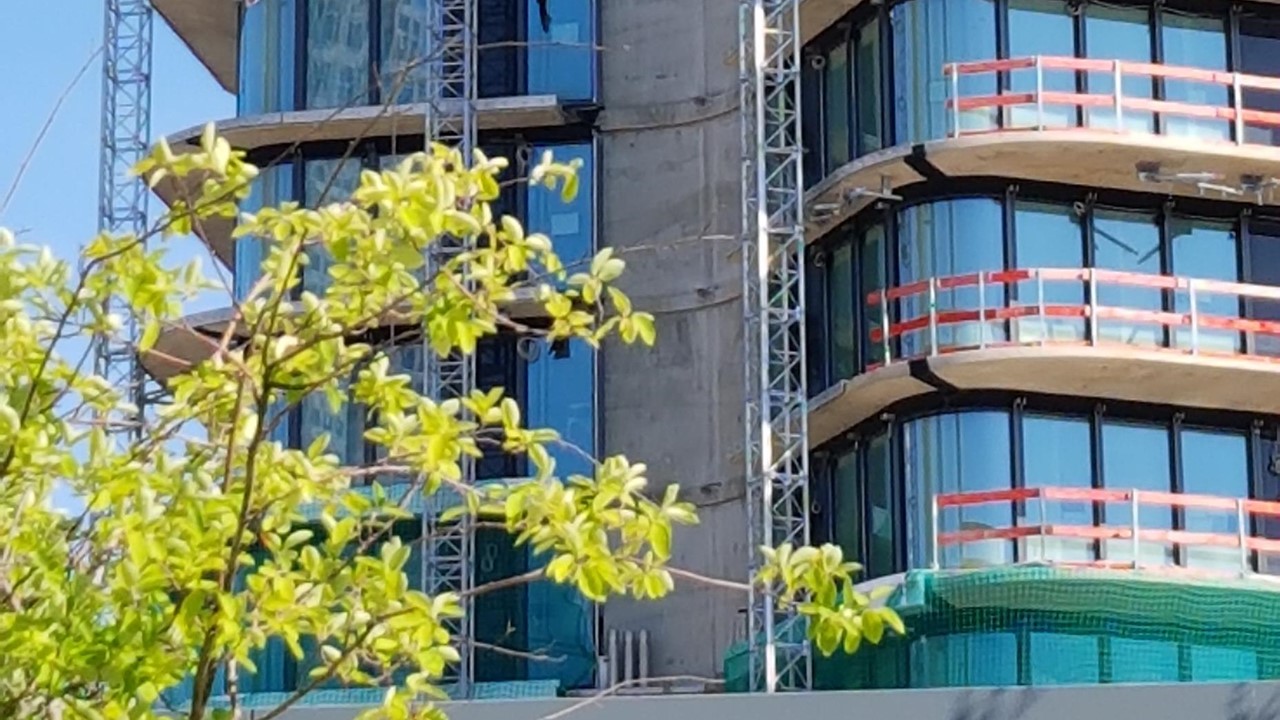
The Challenge
The population in many large cities has been exploding for years. At the same time, there is limited space, therefore every square meter of residential and commercial area counts. The increasing condensation of inner cities has led to a rising demand for innovative insulation materials that are not too thick. The Grand Tower Frankfurt is a prestigious residential building in Germany of 172 meters and 401 apartments whose façade has recently been insulated with Vacuum Insulation Panels (VIPs). The main challenges encountered were achieving a considerable reduction of space and insulating the façade’s many organically shaped units called ‘tubes’.
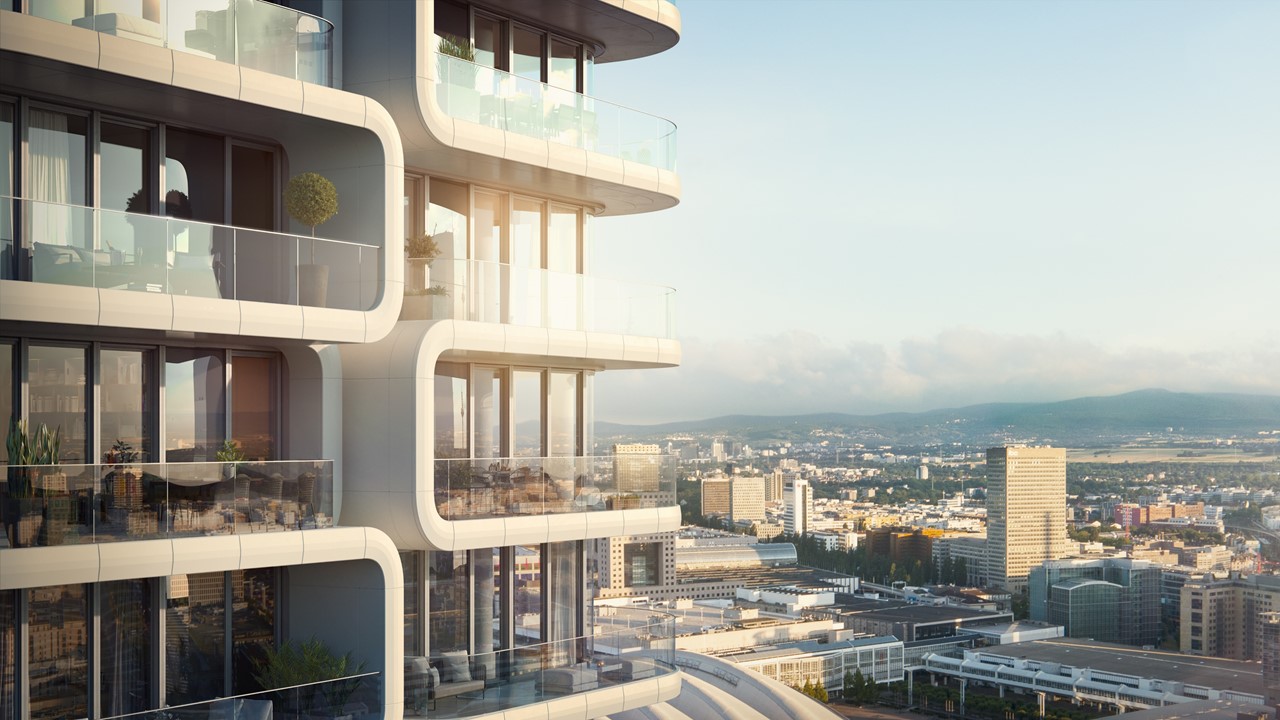
The Solution
The building has been insulated with VIPs in the sections of the façade where supply shafts narrow down the available space considerably. The pressure-resistant core material of the VIPs that have been used is made of a pressed, micro-porous powder. Its inside has been gas-tightly packed in a high-barrier film and evacuated, i.e. emptied of air. These VIPs were only 50 mm thick, while common insulation panels would have been 250 mm thick in order to achieve identical low-energy values. This difference makes up a little less than three square meters of living space per floor in the Grand Tower. In addition, curved VIPs have been developed in order to insulate the many organically shaped units of the façade, called ‘tubes’. This requirement posed a greater challenge at first, as curved VIPs needed to be developed for this purpose.
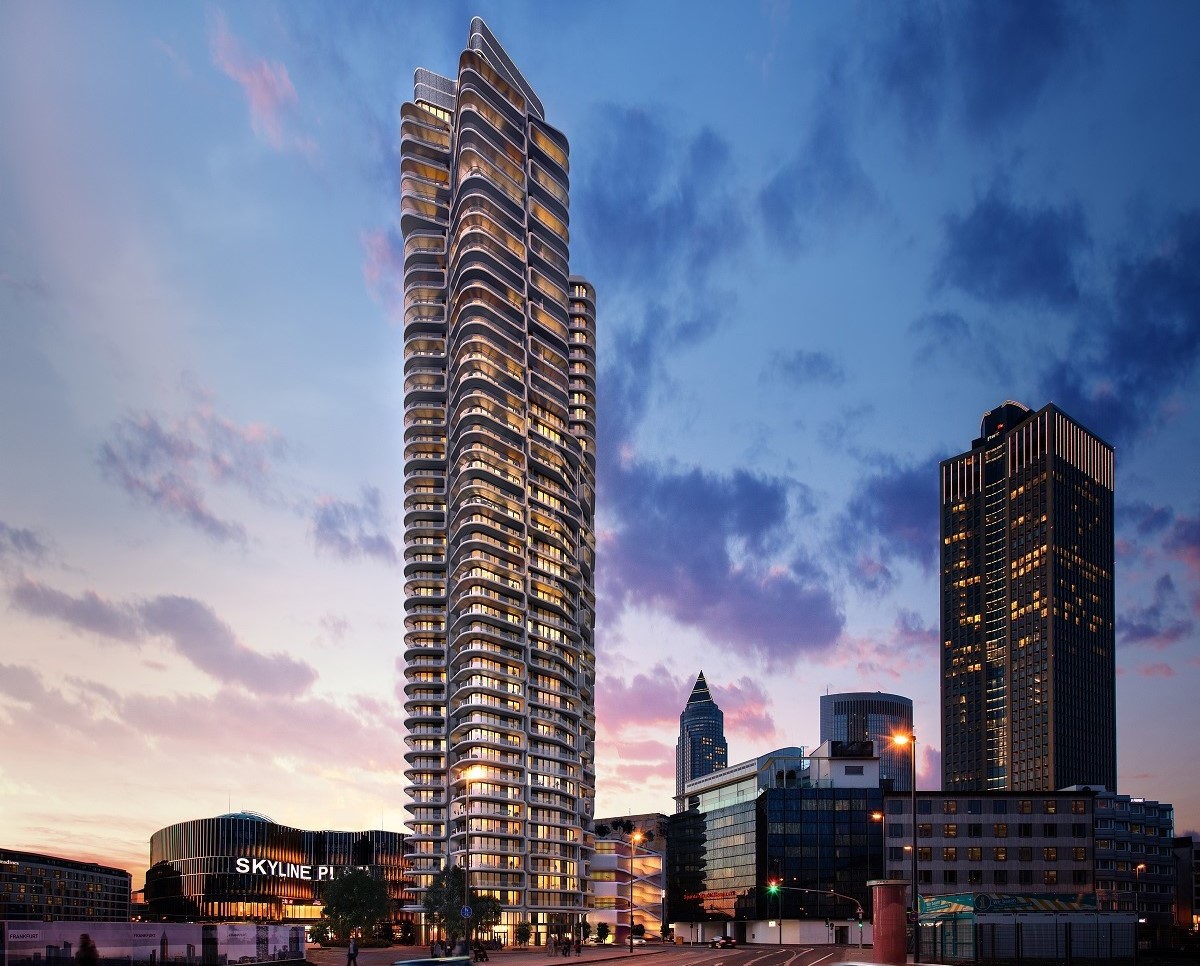
The Result
At 47 floors, the space saved totals up to about 123 m². This corresponds to one spacious apartment, which is valuable around 1 mio Euro in a booming inner city like Frankfurt. VIPs insulate about five times better than conventional insulation materials of the same thickness can.
Based on the measured values of the newly produced VIPs, the panels are even ten times better. Architects and planners can save about 80% space and the lower heating demand also improves the carbon footprint.
Case study provided by va-Q-tec
Download the document
pdf – 295 KB